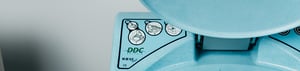
Why Use A Cleaning Efficacy Test For Your Washer Disinfector?
Washer disinfectors are essential to keep reusable bedpans safe for service users.
Often in high demand and used multiple times a day, plastic and stainless-steel bedpans are part of day-to-day life in many hospitals and care homes.
Due to their usage, bedpan hygiene must be carefully managed. Thorough disposal of waste, followed by scrupulous cleaning, is essential to prevent the spread of dangerous HCAIs; without such practices, your service users and clinicians could find themselves desperately unwell, with infections spreading rapidly throughout the facility.
Proper use of a washer disinfector will help to ensure that bedpans are fully cleaned and sanitised, before being passed on the next user. However, it’s essential to make sure that your bedpan washer is always working to 100% efficiency, or dangerous pathogens could still cross-contaminate your utensils.
A visual inspection of bedpans can rarely guarantee adequate disinfection.
Your bedpans may appear to be spick and span, but germs don’t always hide in the dirt you can see. Significant amounts of bacteria (or even residual chemicals) can be invisible to the naked eye, but still thrive; therefore, the only way to be confident that your washer disinfector is doing its job is to validate its performance with regular, documented tests.
You should always be able to provide evidence that your washer disinfector works to standard under specified conditions.
To make sure that silent operational failures don’t slip under the radar, scheduled test programmes should be regularly undertaken by machine users, as well as a trained technician.
A daily test, as performed by a user, should include:
- An automatic control test
- Spray arm rotation check
- Spray nozzle blockage check
- Removal and cleaning of strainers/filters.
Tests at quarterly and annual intervals should ideally be carried out by a maintenance technician, who can perform more in-depth examinations. This includes thermometric tests for disinfection, chemical dosing and general functioning of the operating cycle; all of which will give you the peace of mind that your washer disinfector is running at optimum performance.
A quarterly soil test will not only ensure cleaning efficacy, but also help you adhere to HTM 01-05 recommendations.
A soil test should always be carried out as per the manufacturer’s guidelines (to prevent misleading results) and is performed by a specialist engineer as part of HTM validation testing. The aim of the test is to ensure that the cycle will adequately clean a heavily soiled load and is actioned with a strip coated in an artificial test substance.
The strip represents a particularly difficult level of soiling, which the machine must clear in order to pass the test.
Validation testing is vital to ensure that the machine is working to the high standard that you expect.
What should you do if your machine fails an efficacy test?
If your washer disinfector fails to fully clear a test soil, it’s likely to indicate an underlying operational issue.
A washer disinfector which fails this test should be immediately removed from service and investigated, to protect both your clinicians and service users from a potential HCAI outbreak. What happens next is ultimately a matter of judgement; if you deem the washer disinfector safe to use under certain circumstances, it could continue to operate under controlled conditions. However, it’s most likely that the washer disinfector will need to cease operation and await repair.
Whichever action you choose, it’s ultimately the user’s responsibility to ensure that the machine is safe to use, before continuing to employ it for essential infection control tasks.
A Planned Preventative Maintenance package from DDC will help to keep your washer disinfector in excellent operational health.
DDC can service and maintain any make or model of washer disinfector, thus preventing unpredictable periods of downtime.
Should a machine fault occur, DDC’s expert team of technicians will reach you quickly, thanks to unparalleled UK coverage; with such a large, specialist network, there’s no need for long waits and exposure to bacterial hazards.
Available with a series of service levels, a Planned Preventative Maintenance package will not only help to ensure that your machines always work to their best ability, but also allow your facility to efficiently budget for maintenance costs.
In addition, the regular service pattern available with PPM will equip your facility with detailed maintenance records, for complete audit and CQC inspection transparency.
Better yet, our 360° Care Cover options will provide all-round protection from extra maintenance costs, from the moment you purchase your machine.
The package includes:
- 5 years’ parts and labour warranty with your machine purchase
- Service and maintenance visits over 5 years
- Chemical dosing systems, lockable cabinet and chemical supply
- Machine installation and commissioning
- Staff user training
- Carriage and packing
- Pre-installation site survey and sluice room health check
- Starter pack of bedpans and urinal bottles
- Wall storage rack.