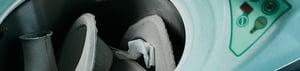
Macerators For Hospitals: 5 Unexpected Benefits
Hospital staff are in a constant battle against waste.
Associated with the risk of infection, injury and pollution, medical waste must be diligently managed in order to protect patients, staff and the wider community. Fortunately, the technology available to streamline this task – making waste management quicker, easier and safer – continues to improve.
Of course, medical waste doesn’t just involve dressings, syringes, drugs and chemicals. Human waste is a vector for many infections, including clostridium difficile, norovirus and COVID-19 – and its near-continuous presence in the care environment, especially when patients are bedridden, presents a minute-by-minute challenge for clinicians.
In the quest to continuously improve how hospitals manage human waste (and its associated utensils, such as bedpans and urine bottles), the medical pulp macerator has become nothing short of a healthcare hero.
Clinicians no longer need to grapple with the unsanitary, time-consuming, and costly task of washing bedpans by hand. Instead, a single-use pulp container can be safely used and disposed of in minutes.
What Is A Hospital Macerator?
A hospital macerator provides a fast and safe method of human waste disposal, whilst simultaneously delivering passive safety measures - such as hands-free operation and antimicrobial surfaces - to minimise the risk of infection.
When the lid of a macerator is opened (usually by a hands-free foot pedal or sensor), the pulp container along with its contents can be placed inside, without the need to wash or dispose of items elsewhere.
The medical pulp container and its contents are then pulverised into tiny particles, with the remaining slurry discharged into the main sewage system. A steady flow of water to the drain removes all waste, as well as preventing blockages and residue build-up in the pipes.
The whole process is complete in as little as 65 seconds, providing a pleasing solution for clinicians who must dispose of waste quickly and scrupulously – often countless times a day.
The top-level benefits are significant… but for busy hospitals with multiple patients and staff per ward, the advantages go even further.
Here are five ways a macerator can help your hospital, which you may not have previously considered...
1. Cost savings.
Medical pulp is a cost-effective choice when compared to the price of reusing bedpans that are made of metal or plastic. We’re not just talking about the purchase value, but the long-term costs of time, effort, risk and resources.
If you’re cleaning bedpans by hand, you need to pay for significant amounts of sanitising chemicals, as well as energy to heat the water (which still won’t be hot enough to kill bacteria, lest clinicians risk scalding their hands).
All the while, a valuable clinician will need to spend around five minutes scrubbing each bedpan, when a macerator could have completed the job – to a far safer standard, killing all pathogens – in just two minutes.
If a clinician has four bedpans to scrub, that’s twenty minutes of their shift spent in the sluice room, rather than helping patients in the ward. The ward still needs to be manned, so you’ll be paying for additional staff to make sure every task is covered.
Using a macerator can help you to streamline your labour costs, but that’s not all. Single-use bedpans are undoubtedly more hygienic then cleaning a re-usable counterpart; and by stemming this cause of cross-contamination, you’ll also reduce the risk of HCAI outbreaks.
When a ward is hit with an infection outbreak, the costs begin to spiral. Patients take far longer to recover, as well as requiring more intensive treatment and attention from clinicians – and if the outbreak is not rapidly contained, the whole ward may need to closed and deep-cleaned to prevent further spread.
The cost of equipment, the cost of manpower, the cost of human life. It all adds up.
2. Reduced risk of user error.
For many hospitals, bank staff are essential. Whether covering sickness, annual leave or an influx of demand, temporary cover is often necessary to maintain good levels of care.
However, staff that are unfamiliar with your ward will need to be trained in how to use its machinery – as will any new staff who are new to their role. This creates significant potential for user error, which could result in a machine needing repair.
The latest macerators are designed to prevent user error as best they can, which in turn will reduce the cost and inconvenience of breakdowns.
The Pulpmatic Eco+, for example, features a Graphical User Interface. By providing animated operation instructions, cycle status information and fault resolution guidance, every clinician is able to use the machine with ease.
That’s not all. Every Pulpmatic macerator is equipped with audio annunciation, which provides helpful voice guidance in any language - decreasing costly training requirements and reducing the number of staff errors.
3. Increased sustainability.
When considering maceratable bedpans that are single use, you might worry that this is a wasteful process which could harm the environment. Don’t panic - this couldn’t be further from the truth.
Pulp is environmentally friendly and made from sustainable materials. After waste is pulverised by the macerator and flushed into the sewerage system, sewer pipes transport the waste to a water treatment plant. Pulp is then filtered out of the water into ‘sludge’, which is turned into agricultural fertiliser.
It’s a very green process which, when paired with the low energy use of the macerator itself, forms an eco-friendly approach to waste management.
4. Improved versatility.
Pulpmatic macerators can be used in various environments, be it a sluice room or a private patient room.
Large-capacity machines, such as the Pulpmatic Ultima, are ideal for sluice rooms in busy wards - while a more compact machine, such as the Pulpmatic Uno, can fit neatly into an isolation room or ICU.
To aid infection control, it’s beneficial to have your macerator close to the point of care – and Pulpmatic machines are designed to make this option as easy as possible.
Noisy machinery can disturb patients and hinder their recovery, whilst also contributing to clinician fatigue. That’s why every Pulpmatic can be equipped with bespoke noise reduction - including the Eco+, which is armed with antivibration dampers and energy-absorbing materials.
In turn, you can ensure that your hospital is supported by macerators where they’re needed most.
5. More time at the patient’s bedside.
Nursing is a vocation.
You don’t enter into this career because you want to be behind the scenes – you do it because you want to be present, supporting those who need your help. By equipping nurses to spend more time providing hands-on care, you liberate them to do their best work; which is not only fantastic for their personal satisfaction, but for the overall quality of care for patients, too.
Perhaps the most critical, unseen benefit of macerators is that they save clinicians’ time and increase productivity.
As mentioned previously, it can take five minutes to manually clean a bedpan. It’s hard and unappealing work, which simply can’t compare to being at a patient’s bedside.
Over the course of a day, minutes turn to hours – and patients continue to miss out on the quality support of your nursing team.
By using a macerator, the vital job of managing human waste is made quick and efficient. A maceration cycle can take as little as 65 seconds, freeing your clinicians to spend more time with patients on the front line – aiding recovery and saving lives.
The DDC range of Pulpmatic macerators are trusted by thousands of facilities around the world.
We are very proud to have been selected as an NHS preferred supplier – not only for the purchase of macerators, but for the service, maintenance, and validation of every brand of macerator in UK hospitals.
No matter what your macerator requirement is, DDC can help.
The Pulpmatic Ultima is our largest capacity bedpan macerator, suitable for busy hospital wards and care homes, capable of disposing of up to 6 pulp items per cycle.
Its unique nine bladed macerator technology allows for a rapid disposal cycle of just 120 seconds, without compromising on efficiency, water usage or noise levels.
The Pulpmatic Uno is our low-use bedpan macerator for smaller hospital wards and care home environments. Capable of processing 1-2 pulp items per cycle, it provides a quieter, economical solution where maceration is a requirement, but demand is minimal.
The Uno’s seven blade macerator disc provides rapid, low-noise maceration for minimal disruption to a small ward setting, with a cycle lasting just 65 seconds.
The Pulpmatic Eco+ is the most environmentally friendly, economical and hygienic macerator on the market.
Featuring enhanced chemical dosing, powerful antimicrobial surfaces and fully hands-free operation, you can be certain that this sluice machine will prevent the spread of infection in your facility.
It is perfectly suited for medium capacity wards, processing up to 4 pulp items per cycle. Its advanced five blade macerator disc provides rapid, low-noise, finer maceration in a cycle lasting from just 85 seconds – truly leading the way for infection control technology.