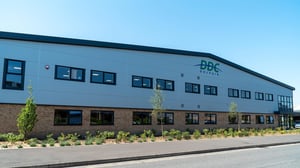
Selecting The Perfect Sluice Room Equipment for Your Facility
Introduction
Choosing the right sluice room equipment is a decision that bears long-term consequences for any hospital or care home. The selection process goes beyond mere purchase; you need a solution that meets the specific needs of your facility, aligns with your infection control protocols, and integrates seamlessly with the daily workflow of your staff.
The right equipment will…
1. Support Your Facility's Overall Hygiene Strategy
The right sluice room equipment plays a pivotal role in supporting your facility's overarching hygiene and infection control strategy. It ensures the safe and efficient disposal of hazardous waste and the disinfection of re-usable medical supplies. Selecting the appropriate machinery - for example, choosing a bedpan washer with a high-temperature thermal disinfection cycle - can help eliminate pathogens effectively and prevent cross-contamination. This alignment with hygiene protocols contributes to creating a safer environment for both patients and healthcare workers.
2. Reduce Downtime
Equipment reliability is key to maintaining continuous operational capacity. Downtime in sluice room operations can cause backups in waste processing and compromise hygiene standards. By choosing equipment that is known for its durability and ease of repair, healthcare facilities can minimise these disruptions. Additionally, equipment with advanced features such as self-diagnosing functions can help predict and prevent malfunctions before they lead to significant downtime, keeping the sluice room running smoothly and efficiently.
3. Ensure Compliance
Healthcare facilities must adhere to strict regulations governing waste management and infection control. High-quality sluice room equipment designed to meet these regulatory standards helps ensure that your facility remains compliant. This includes meeting the guidelines set by organizations such as the Care Quality Commission (CQC) and Healthcare Inspectorate. By doing so, facilities can avoid the costly consequences of non-compliance, including fines, legal action, and potential closure.
4. Enhance Quality of Patient Care
Investing in the right sluice room equipment indirectly enhances patient care by reducing the risk of healthcare-associated infections (HCAIs). Efficient and effective cleaning and disinfection processes ensure that reusable items are safe for patient use. This also shows a commitment to patient safety and care quality, which can improve patient satisfaction and trust in the healthcare system.
5. Increase Operational Efficiency
The right equipment enhances operational efficiency by streamlining sluice room processes. This can include faster cycle times in bedpan washers and macerators, reducing the time needed for staff to manage waste, and allowing them to dedicate more time to direct patient care. Additionally, modern machines often feature user-friendly interfaces and automation, which reduce the learning curve and free up staff to perform other duties. Efficient operations can also lead to cost savings by reducing utility usage and maintenance requirements.
By addressing these aspects comprehensively, healthcare facilities can ensure that their investment in sluice room equipment yields positive returns in terms of maintaining a high-quality care environment and operational excellence.
Key Factors
When selecting sluice room equipment, several critical factors come into play.
1. Facility Size and Layout
The physical attributes of your healthcare facility directly impact the type and scale of sluice room equipment necessary to meet your needs. A small clinic, for example, will have different requirements to a city hospital with numerous departments, generating varying types of waste.
In a large hospital, you may need multiple sluice rooms equipped with high-capacity washer-disinfectors and macerators to manage the volume efficiently. By contrast, a compact care home may only require a single, smaller-capacity unit.
Larger facilities often benefit from a centralised sluice room system that can handle high volumes of waste with quicker processing times, while smaller facilities might opt for decentralised units closer to patient care areas to reduce cross contamination.
The design of the sluice room should also account for the workflow, providing enough space for the safe and hygienic movement of staff and materials.
2. Patient Load
The patient demographic is another key consideration. Different facilities will have different requirements for waste disposal products.
Long-term care facilities will often require robust disinfection processes for a high turnover of bedpans and urine bottles[TH1] , whereas an A&E department may generate more pulp products that need maceration.
It’s essential to assess not just the current patient load but also to anticipate future changes or expansion possibilities. Equipment should be scalable or sufficiently flexible to adapt to increasing or shifting demands, without needing complete replacement – thus futureproofing your investment.
3. Budget
While budget constraints are a reality for most healthcare facilities, short-term savings on cheaper equipment can lead to higher costs down the line due to inefficiencies, more frequent breakdowns, and shorter lifespans. Facilities must consider not only the initial purchase price but also the long-term financial implications, including maintenance costs, energy consumption, and potential downtime costs. For example, investing in a slightly more expensive macerator with a proven track record of reliability may reduce the frequency and cost of repairs.
A cost-benefit analysis comparing different models and brands can help you understand the total cost of ownership. Sometimes, leasing equipment or looking into flexible payment plans can make higher-quality options more accessible.
4. Compliance Requirements
Compliance with regulatory standards is non-negotiable in healthcare settings.
Healthcare facilities in England, for example, must comply with the stringent infection control guidelines issued by the CQC and NHS. All equipment selected must be capable of meeting these requirements. This might include, for instance, washer disinfectors that maintain a specific temperature for a set duration to achieve thermal disinfection, as stipulated by HTM 2030 guidelines.
Compliance also means preparing for future changes in regulations. Equipment that comes with the ability to update or modify programs and functions can adapt to evolving standards, ensuring long-term compliance and avoiding the need for premature replacement.
When navigating these factors, practical examples include…
- Consulting case studies of similar-sized facilities
- Seeking references from equipment suppliers for comparable installations
- Projecting patient load growth based on historical data and community health trends.
By thoroughly addressing each of these factors, healthcare facilities can select sluice room equipment that is fit for purpose, financially sound, and compliant with all necessary regulations - thereby ensuring safe and efficient waste management.
Customisation Options
Sluice room equipment is not a one-size-fits-all solution.
Customisation options are critical to ensuring that the equipment fits the unique demands of your facility. Leading-edge sluice machines can be customised during installation – For example, engineers can customise machines’ software to adjust cycle times.
This approach guarantees energy and water are utilised as efficiently as possible, cutting down on operational expenses annually and consistently meeting the standards for infection prevention and control.
Additionally, tailoring machines to operate more quietly is essential in patient care areas where excessive noise may cause disturbances.
Budgeting for Sluice Room Equipment
Investing in the right sluice room equipment is an investment in your facility's future.
Budgeting for this equipment involves understanding not only the purchase price but also the long-term costs associated with operation, maintenance, and potential downtime. High-quality equipment, while perhaps more costly upfront, often presents greater reliability and durability, leading to lower life-cycle costs.
Considerations for budgeting include:
1. Energy-Efficient Models
When planning a budget for new sluice room equipment, it's crucial to consider the long-term operational costs, which include daily energy and water consumption.
Energy-efficient models, though they may come with a higher initial price tag, are designed to consume less power and water, leading to significant cost savings over the lifespan of the equipment. These savings are not only beneficial from a financial standpoint but also support environmental sustainability initiatives, which can be a valuable aspect of a healthcare facility's corporate social responsibility program.
2. Longevity and Maintenance Coverage
The expected service life of the equipment and the warranty terms are important budgetary considerations.
High-quality sluice room equipment, built to withstand the rigorous demands of a healthcare environment, often has a longer lifespan - which translates into a lower annual cost when spread over many years of service.
Maintenance coverage plays a pivotal role as well; choosing a maintenance agreement that includes regular servicing, quick repair response times, and coverage of replacement parts can prevent unexpected financial outlays.
A well-structured maintenance plan can not only extend the life of the equipment but also maintain its efficiency and reliability, which are essential for uninterrupted sluice room operation. Evaluating the total cost of ownership by including maintenance provisions offers a more accurate financial projection and secures the operational budget from the volatility of ad-hoc repair costs and the associated administrative burden of managing unpredictable maintenance issues.
3. Training and Support Offered for Installation and Use
The level of training and support a supplier provides can be a determinant of how smoothly your sluice room operations are integrated and maintained.
A good supplier will offer thorough training for your staff on how to use the new equipment safely and effectively. This training is essential for ensuring that equipment is used in a way that maximises its efficiency and lifespan while maintaining safety and compliance standards.
Post-installation support is equally important; suppliers should provide a clear plan for ongoing maintenance and technical support, including how to handle potential faults or required upgrades. Support offerings might include regular service visits, a help desk for immediate advice, and remote troubleshooting to reduce downtime. These services help to maintain the continuity and quality of care that patients expect from your facility.
Evaluating Suppliers
Selecting a supplier for your sluice room equipment is a process that should be approached with as much care as selecting the equipment itself. A reliable supplier will have a strong reputation in the industry, provide comprehensive maintenance services, and offer excellent after-sales support.
It’s advisable for suppliers with a track record of delivering quality equipment to healthcare facilities with a similar scope to your own.
When evaluating suppliers, consider:
1. Understanding of Healthcare Compliance and Hygiene Standards
When selecting a supplier for sluice room equipment, it's important to assess their expertise in healthcare compliance and hygiene standards. A supplier with a deep understanding of the regulatory landscape ensures that the equipment they provide meets all the current legal and safety requirements.
This knowledge is crucial for protecting patients against HCAIs and safeguarding your facility against compliance risks. Suppliers should be well-versed in national standards - such as those from the Department of Health, NHS directives and CQC guidelines - as well as international standards where applicable.
They should also be proactive in anticipating changes to these standards and advising on how to adapt to them, ensuring a futureproof investment for your facility.
2. Reliability and Service Excellence
A supplier’s track record in reliability and service excellence is indicative of the performance you can expect. Investigate the supplier's history by looking for customer testimonials, case studies, and reviews that may provide insights into their reliability.
Long-standing suppliers with a proven record of delivering high-quality equipment on time and to specification are often the most reliable choices. Additionally, suppliers with a commitment to service excellence typically offer comprehensive support and are responsive to customer needs, ensuring any issues are promptly and effectively resolved. This reliability can significantly reduce the risk of equipment downtime and the associated operational disruptions.
3. Training and Support for Installation and Use
The level of training and support a supplier provides can be a determinant of how smoothly your sluice room operations are integrated and maintained.
A good supplier will offer thorough training for your staff on how to use the new equipment safely and effectively. This training is essential for ensuring that equipment is used in a way that maximises its efficiency and lifespan while maintaining safety and compliance standards.
Post-installation support is equally important; suppliers should provide a clear plan for ongoing maintenance and technical support, including how to handle potential faults or required upgrades. Support offerings might include regular service visits, a help desk for immediate advice, and remote troubleshooting to reduce downtime. These services help to maintain the continuity and quality of care that patients expect from your facility.
Buyer FAQs: Selecting Sluice Room Equipment
To select the right sluice room equipment for your facility, conduct a comprehensive needs assessment considering patient volume, waste types, and space constraints, and ensure the equipment complies with healthcare regulations. Then, collaborate with reputable suppliers to explore options, request demonstrations, and consider the total cost of ownership, including maintenance and potential upgrades, to make an informed, forward-looking investment.
To select the right sluice room equipment for your facility, conduct a comprehensive needs assessment considering patient volume, waste types, and space constraints, and ensure the equipment complies with healthcare regulations. Then, collaborate with reputable suppliers to explore options, request demonstrations, and consider the total cost of ownership, including maintenance and potential upgrades, to make an informed, forward-looking investment.
To balance quality with budget constraints, focus on the total cost of ownership rather than just the upfront cost of sluice room equipment. Analyse data sheets provided by suppliers for information on efficiency, durability, and servicing needs, which can help you understand long-term savings and value. Investing in higher-quality equipment may result in lower lifetime costs due to reduced energy use, maintenance needs, and better infection control outcomes, offering a more cost-effective solution over time.
Selecting the right sluice room equipment necessitates a balanced approach that considers immediate needs and long-term efficiency.
By understanding your facility's specific requirements, budgeting wisely, and choosing a reputable supplier, you can ensure that you invest in equipment that enhances your healthcare facility's hygiene and compliance, contributing to better patient outcomes and streamlined operations.