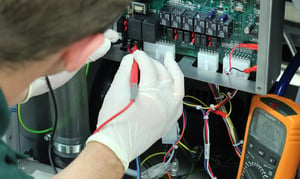
Sluice Machine Breakdowns: The Real Cost (and How to Avoid It)
Impact of Sluice Machine Breakdowns
There is never a good time for any machine to fail. But when a medical pulp macerator or bedpan washer disinfector breaks down, the infection-control consequences can be extremely severe.
Failure to prevent or contain any resulting infection outbreak can lead to the temporary closure of a hospital ward pending emergency deep cleaning. And care homes can be equally vulnerable – as the pandemic tragically proved.
Hospital patients or care home residents are put at risk when a vital infection-control sluice machine stops working.
What starts as a mechanical inconvenience could end in cross-contamination, failure in duty of care, reputational damage, breaches of compliance and even personal injury litigation – with all the associated financial fallout.
Fail to maintain your sluice room equipment properly and you risk a higher incidence of breakdowns – up to three times per year on average. Costs soon spiral upwards. They can be disproportionately high when compared with the price of servicing a machine.
With DDC’s Managed Service, hospitals can achieve seamless infection control without any capital outlay. This all-in-one approach includes state-of-the-art equipment, proactive maintenance and expert infection control support – delivered in one predictable monthly payment for complete peace of mind.
High Cost of Replacing Machines Early
Our service engineers don’t just work on DDC-manufactured medical pulp macerators and bedpan washer disinfectors: they service and repair all the other brands too. So we know what causes those machines to fail, enabling us to design machines without those flaws.
But – just like a car – every sluice machine needs proper servicing to ensure optimal performance. Just 1 mm of limescale can increase a bedpan washer disinfector’s energy consumption by 11%. If left unchecked, this limescale can cause a breakdown. Machines in hard water areas are at greater risk for obvious reasons.
Without regular servicing, a sluice machine will typically last seven years. But with the right pre-planned maintenance, a machine will provide dependable service for 10 or more years.
Based on purchase price alone, a machine that lasted just seven years and had to be replaced would result in your paying 42% more over a 10-year period.
And that’s without considering inflation and the inevitably higher price of a replacement machine after seven years.
Multiply that 42% higher cost by all the machines in your hospitals or care homes. All that expense does not bear thinking about. Or rather it does, so invest in a good reliable machine and have it properly maintained. You will enjoy substantial savings and priceless peace of mind.
With Managed Service, you also avoid the challenge of sourcing capital to replace aged machines. Instead, you gain continuous access to the latest infection control technology through a cost-effective payment plan – helping you manage budgets more effectively while enhancing brand reputation with new, innovative equipment.
True Cost of Sluice Machine Breakdowns
Servicing should never be viewed as a cost. It is an investment that will extend the life of your machines – saving you far more money in the long run. It is important to focus on the whole-of-life ownership savings, which will far outweigh the pre-planned maintenance spend.
Decades of experience have proven this time and again. Here are the numbers:
- Estimated cost of a breakdown (without a service contract), £548 per visit
- Estimated cost of a breakdown (with a service contract), £313 per visit.
Machines that are not serviced properly will almost certainly break down. Aside from the infection control risk, the consequences include increased downtime, lost productivity and unplanned call-out charges.
The difference is £235 per visit. Multiply that by an average three breakdowns per year, and then by the number of machines you have. Again, the costs soon build up. And worst of all, this financial waste could so easily have been prevented. It need not have happened.
DDC’s Managed Service proactively prevents downtime through planned maintenance and 24/7 support. With reduced repair costs, optimised servicing schedules and potential VAT reclaims, hospitals benefit from predictable fees that save money long-term while maintaining safety and compliance.
Counting The Cost of Operator Error
Unfortunately, many machine breakdowns are caused by user error. It happens with alarming regularity, despite the fact that machines are simple and intuitive to use, with graphics-based displays/controls to overcome language difficulties.
This is why staff training is so important.
How User Error Can Damage Macerators
Macerators are frequently subjected to mistakes that reduce their lifespan, cause breakdowns or introduce infection risks. Here are the most common errors:
Incorrect Loading of Materials
Issue: Staff place inappropriate items in the macerator. These can include gloves, wipes, incontinence pads, plastic utensils or syringes.
Consequence: These items can’t be shredded properly and cause blockages, blade jams or pump failure. It’s a common cause of downtime and costly repairs.
Overloading
Issue: Too many pulp items are placed in the chamber. Or they are too large.
Consequence: This strains the motor and blades, leading to incomplete maceration, clogs in the outflow system or cycle failure.
Skipping Pre-Use Checks
Issue: Operators do not check for leftover debris from previous cycles (or don’t notice warning indicators).
Consequence: Ignoring these checks increases the risk of blockages, mechanical wear and progressive damage that often goes unnoticed until a breakdown.
Not Using the Correct Cycle
Issue: Using the wrong button or interrupting the cycle prematurely.
Consequence: This can result in incomplete disposal, drainage issues or malfunction if the system is not allowed to reset properly.
Neglecting Clean-Down Procedures
Issue: Routine internal cleaning (often a simple rinse or flush cycle) is ignored.
Consequence: This leads to the build-up of pulp residue, odours and bacterial growth. There is an increase in mechanical resistance, which can damage internal components over time.
With a Managed Service, comprehensive training and support help staff avoid these common mistakes. This not only protects machine reliability but also boosts staff productivity, morale and infection control standards. After all, breakdowns don’t just halt equipment – they disrupt workflows. Staff time is lost while they wait for repairs or switch to less efficient manual processes, creating additional stress and - ultimately - impacting quality of care.
How User Error Can Damage Bedpan Washer Disinfectors
Bedpan washer disinfectors can be more complex than macerators, requiring greater operator understanding. However, many issues stem from basic oversights or lack of proper training. These are common errors:
Improper Loading Technique
Issue: Bedpans and urinals are loaded incorrectly – facing the wrong direction, stacked on top of each other – or the machine is overloaded.
Consequence: Water and disinfectant can’t reach all surfaces, compromising cleaning and disinfection effectiveness.
Failure to Rinse Soiled Items
Issue: Faeces or thick bodily fluids are not pre-rinsed away before loading.
Consequence: This causes blockages in spray arms and jets, reduces cleaning effectiveness and increases the risk of foul odours and infection.
Interrupting or Skipping Cycles
Issue: Users open the door mid-cycle or cancel the programme to save time.
Consequence: Items are not fully disinfected, breaching infection-control protocols and risking the safety of patients/residents and staff.
Incorrect Detergent or Disinfectant Use
Issue: Staff refill the machine with unapproved chemicals or water down detergent to stretch supply.
Consequence: This can cause internal corrosion, sensor faults and sub-standard disinfection performance.
Ignoring Error Messages or Service Lights
Issue: Operators assume that alerts are minor or temporary and continue using the machine.
Consequence: This leads to unreported faults developing into serious failures, requiring the emergency intervention of an engineer.
How To Cut The Cost of Sluice Room Maintenance
It may seem easier and more cost-effective to address issues as they arise but the reality is very different. Playing the reactive game is a false economy that will cost you significantly more in the medium and long term.
Proactive maintenance is the prudent option. It reduces downtime, minimises disruption and helps to avoid unexpected expenses.
Servicing is also the only way to ensure effective infection prevention and control – which is the whole point of investing in this equipment in the first place.
DDC’s Service Package includes:
- reduced pricing on servicing call-outs and spare parts
- rapid response – fast support when you need it
- minimised downtime – keep machines running smoothly
- lifetime support – expert help throughout your equipment’s lifespan
- stress-free maintenance – avoid disruption and staff downtime
- expert planning – tailored maintenance schedules
- CQC compliance – regular testing and servicing helps you to stay compliant
- training included – practical in-service training for your team.
Our Managed Service builds on these advantages, delivering enhanced reliability and safety, reduced downtime and access to DDC’s infection control expertise – all without capital outlay. Hospitals can focus on patient care while we handle every aspect of equipment management, from supply and installation to maintenance, upgrades and compliance documentation.
Investing in high-quality sluice room equipment and proper servicing is essential for controlling infections, minimising downtime and protecting budgets.
With DDC’s Managed Service, hospitals gain seamless access to innovative technology and expert support without any upfront capital outlay.
Aligned with NHS Supply Chain’s guidance on Managed Services, this approach delivers predictable costs, transfers operational risk to experienced specialists and ensures that equipment remains safe, compliant and reliable.
By adopting this value-based procurement model, hospitals can:
• Improve infection prevention and patient safety.
• Enhance operational efficiency with minimal disruption.
• Benefit from long-term cost savings and sustainable resource management.
With proactive maintenance, rapid response servicing and complete peace of mind included, DDC enables hospitals to focus on delivering exceptional patient care while we handle every aspect of sluice room management.
More Information
Find out more about DDC's Hospital Sluce Room Management solution.